Pipe and riser irrigation systems
It is strongly recommended before you make the decision to purchase any pipe and riser system you identify your individual requirements. This will help guide your decision in relation to the type of equipment you purchase.
Installation of this type of equipment is a significant business decision and growers are encouraged to do a financial assessment that appropriately considers the investment. This should consider:
- cash flow impacts
- capital expenditure versus operation and maintenance
- payback period
- tax implications
- benefits (productivity and labour) of the investment.
It is important you seriously consider the alternatives such as earthen channels.
Given the appropriate soil conditions, design, construction, operation and maintenance, channel systems can be cost effective and efficient. Talk to an irrigation surveyor and designer to ensure a pipe and riser system is right for your particular situation.
Once you are certain a pipe and riser system is what you want or need, consider the following.
Flow rate (or discharge)
What flow rate do you want or need? Generally the response is in the range of 1220ML per day. The answer to this helps to determine the diameter of pipe required and the likely pump specifications.
You should seek advice from an irrigation surveyor and designer to ensure the flow rate meets the requirements of the farm's physical characteristics and/or the crop being grown.
It is important the flow rate matches the crop's requirement, that is, it adequately fills the root zone. Too small a flow rate may mean water ponds too long pushing past the root zone and contributing to deep drainage. Too large a flow rate may result in water not infiltrating deep enough to satisfy the crop being grown resulting in lost production.
You should do a Whole Farm Plan (WFP) (or modify their existing one) to reflect the pipe and riser system design. This will ensure the system is compatible with the proposed layout as detailed on the WFP and considers future expansion.
Length, shape or layout of the pipeline
The answer to this will help determine the diameter of pipe required and the likely pump specifications. In addition you might want to install a system on part of the farm and expand the system later. This needs to be considered now. If expansion is not considered initially and you want to do it later the system will be too small and require significant modification, or even a complete new system.
It is not common for systems to be a simple straight length of pipe, they often have pipe teeing off and may be looped to satisfy the physical layout of the property. This will influence the pipe size and pump specifications and highlights the importance of proper design and consideration of all options during the design phase.
How many bays to irrigate at the one time
Suppliers suggest ideally one bay at a time should be irrigated to ensure a cost effective system that meets the requirements of the crop being grown.
The more bays you want to irrigate at once the greater the demand on the system so the pipe and pump specifications will need to be altered. It will impact on the flow rate and the ability of the system to deliver the correct application rate to satisfy the crop being grown without losing water from the production system, (deep drainage beneath the active root zone). It is also difficult to deliver the same flow rate out of two risers at the same time which could lead to inefficient irrigation on one or both bays.
If automation is something you are considering, remember it is easier to automate irrigation if one bay is irrigated at a time.
Once these considerations are known, the supplier or designer is able to determine the pipe size required to deliver the required flow rate.
Ongoing operation cost per ML
This is one of the most important considerations you will need to make. A relationship exists between pipe size, pump efficiency, head loss and energy costs that will impact on the cost to pump a ML of water for the life of the system. If you get this wrong, the overall cost (capital expenditure plus operation and maintenance) will be significantly higher than it needs to be.
You should always aim to design a system that delivers the required flow whilst minimising energy requirements. This ensures the system remains as economically efficient as possible for the life of the equipment.
Using a gravity system
Gravity systems can be installed (a system that does not require a pump) but significant head is required that is rarely obtainable in northern Victoria. The head required would need to be greater than approximately 1 metre for these systems to adequately meet irrigation requirements.
If you have suitable head then this option should be discussed with your irrigation surveyor and designer or pipe supplier.
Determining pump efficiency
Pump efficiency is a complex relationship that will vary due to a range of factors including:
- impeller/pump design and type
- impeller diameter
- total head
- speed and flow rate.
All reputable suppliers will have curves that demonstrate their pump efficiencies. It is important you ask to see these and understand them so you can determine which pump provides the flow rate you require at the highest possible efficiency.
The higher the efficiency the more water it will move per watt of energy.
Also consider the efficiency of the pump across the full range of the system — that is, how it performs at the closest, furthest and all risers in between.
Head loss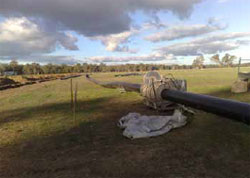
Head loss is the total hydraulic resistance against which the pump must operate (friction). It means the effort required to push water through the pipe and deliver the required flow rate at the furthest outlet/riser. It is described as metres of head at the pump. The simplest way to reduce the head loss is to increase the pipe size.
The aim is to design a system that results in a head loss of between 5 and 10 metres.
Often smaller pipes are installed to reduce the capital cost. This decision creates a higher head which is overcome by upgrading the pump/motor set. However, the higher the head the higher the pressure required to deliver the flow rate. This may result in problems with leaks, especially around closed risers, and will result in higher pumping/energy costs.
Level of flexibility required to be built into the system
Flexibility should always be a consideration in the design phase — such as:
- variable speed drives
- expansion at a later date
- increased flow rate
- automation.
This is best done as a component of a WFP. A number of designs should be done to show the full range of flow rates for various options. If the limits are pushed there is very limited flexibility once the system has been installed.
It is critical at the start of the process irrigators seriously consider what they want to have in the long run. It is costly to make changes once the system is in the ground. This includes simple things like retro-fitting automation. In many instances this cannot be done without major modifications if the system has been installed without prior planning.
Pipe and riser systems provide irrigators with greater flexibility in which bays get irrigated. A single bay can be irrigated one day and another on the opposite side of the system or farm can be irrigated straight afterwards. Traditional channel systems are less flexible as groups of bays often need to be irrigated one after the other to take advantage of the channel being filled.
Looped system
Normally a single pipe leaves the pump and moves through the property to deliver water out of the risers to the irrigation bays. A looped system has two pipes that are joined somewhere on the property to form a "loop".
Looped systems are used to reduce the size of pipe required to deliver the necessary flow rate. It is important bays can be irrigated on all lengths of the system to avoid dead lengths of pipe. These systems are able to deliver the required flow rate at all spots along the pipeline.
It is not possible to install looped systems in stages, they need to be fully installed. Keep this in mind if you are considering staging installation over time.
Capital expenditure versus operation and maintenance
It is possible to reduce capital expenditure by using a smaller pipe and increasing the size of the pump/motor set required to deliver the desired flow rate. For example, to increase the pump/motor size on a pump may cost $1000 (subject to power requirements and pump specifications) while , to increase the pipe size from 355mm to 400mm may cost $10,000 for approximately 1km of pipe. This needs to be given careful consideration because operation and maintenance costs will be greater. Also future expansion and system flexibility will be limited if the pipe is too small.
If the volume of water being pumped through the system each year is relatively small, additional consideration may be warranted. Some people will argue you can compromise on some of the other factors such as the pump/motor set if this is considered against the capital cost over the life of the project. The reduction in capital cost may mean additional pumping cost per ML results in a net benefit across the life of the system.
Velocity
Ask what velocity the system is designed to operate at. If it is greater than 2 metres per second (2m/s) you need to understand why, as it may be uneconomic long term due to higher operating and maintenance costs.
Diesel or electric motor
Often there is no choice because it is too costly to connect power but if you have an option, there are some subjective and economic considerations. To help make this decision ask your designer to provide an estimate of the pumping costs for both options and what the capital costs would be. Depending on the volume of water you plan to pump each year it may be attractive to install a diesel motor. Also consider such things as:
- refuelling diesels
- bunding around fuel tanks
- automation
- safety
- greenhouse impacts
- operating life and general maintenance requirements.
Riser size
Consideration should be given to the size of risers you would like to install. For example a 450mm pipe should have a 400mm riser.
Installing smaller risers will result in increased operation and maintenance costs because of head loss and problems associated with wash when water is delivered onto the bay.
Install as big a riser as possible to help alleviate these problems but remember ease of construction will affect cost.
It is harder to install a riser the same size as the pipe than one that is a size smaller than the pipe.
Variable speed drives (VSDs)
VSDs provide growers with flexibility and reduced energy consumption. They are an electronic device that allows the speed of the motor to be accurately controlled meaning growers can speed up or slow down the application of water from the pump/motor set. They allow the grower to control the flow rate at any point in the system.
Shrouds
Are often used on risers to ensure they can be opened and closed without the operator getting wet. This can increase wash as the water is directed to a smaller area (more energy on a smaller footprint).
Suction pipe
Suction side of the pump needs to be considered especially if there is some distance between the pump and the supply point. It is possible that on start up the pipe may collapse. This weakens the wall and can only be fixed by removing the damaged section of pipe. To prevent this, heavy walled pipe should be installed and/or a pump pit or a mechanism to allow the pump to be started at lower speeds.
Flooded supplies
Conversely flooded supplies (where the water level on the supply side of the pump is higher than the pump) may need additional engineering solutions to protect the equipment. For example, a surge tank may be required when shutting down the system to deal with the energy of the water in the suction pipe.
Pipe joins and welds
Some companies identify each weld with a stamp ensuring welds are completed by certified technicians to Australian Standards.
Ensure your supplier meets this standard and ask to see their technician's qualifications. Adhering to correct procedures that are to the Australian Standard will ensure welds are as strong as possible prolonging the life of the system.
Other sources of water
Dairy effluent can be pumped through these systems and this will be of benefit to some irrigators. Similarly other supplies such as groundwater may be pumped through the system. These alternative sources of water may be harsher on the system and appropriate shandying and engineering solutions should be employed to minimise any impacts.
Reuse and channel connections
Reuse and channel connections may require a one way valve to prevent the channel being emptied to the reuse and vice versa. This might be especially important if you are using effluent through the system.
Trenching and backfilling
You should consider trenching and backfilling during the installation of the system. It is best if this is done to a specified standard which is agreed up front, so problems associated with poor backfill material is eliminated.
Some pipe supply companies prefer pump and excavation work is considered and contracted separately to the pipeline. This ensures growers have a relationship with the pump supplier and excavation company so they get expert advice and have someone to go to if they have problems relating to these specific aspects.
Opening and shutting risers
There are two ways a riser can be open and shut — manual or automatic. A range of options exist within these categories and these include:
- Manual — the irrigator approaches the riser and manually opens or shuts the riser using a handle attached to a screw.
- 12 volt — a motor is attached (permanent) to the screw mechanism. The irrigator carries a battery and attaches leads to the motor. This is used to open and close the riser.
- Timers — can be attached to the 12 volt openers to close and open risers at a predetermined set time.
- Permanent batteries and solar panel — can be attached to each riser, a button is pushed to open and close the riser.
- Full automation — risers can be fully automated to open and close.