Free standing cat enclosure
Cats love to move around and keep watch over their territory. They need a warm dry bed and somewhere to laze in the sun. By building your own cat enclosure you can tailor it exactly to the needs of your cat. Cats love the variety that this system of enclosure provides, especially if it is linked to the family home through a cat door.
To help you design the layout to suit the space that you have available, our instructions include different sections that you can mix and match to make the perfect enclosure:
- how to build a basic enclosure
- add on auxiliary enclosures
- linking tunnels.
Basic design considerations
- Cats must have shelter from sun, wind and rain. They also need a sunny spot within the enclosure.
- Cats must have a weatherproof sleeping compartment with a raised bed (which must be kept in a clean and hygienic condition), along with a separate exercise area.
- The cat litter tray area must be well away from the cat's eating and sleeping areas. It must be kept dry and be easily cleaned. Litter trays must contain an appropriate litter material and be cleaned daily (many cats will not use soiled litter, and will therefore soil elsewhere in the enclosure).
- Disinfectants containing phenol must never be used around cats.
- To prevent disease, your cat must be regularly wormed and vaccinated (as per veterinary recommendations), and flea control must also be undertaken. Accommodation should provide good ventilation, as this is vital to prevent build up of odours that can cause breathing problems in cats.
- Hygiene and odour shouldn't be a problem as long as your cat uses its litter tray and the tray is cleaned regularly. However, you could consider adding flooring in case your cat soils the ground inside the enclosure. This could be as simple as installing small gauge wire mesh on the floor, to prevent cats from digging and soiling in the dirt. Alternatively, you could install concrete or timber flooring that will be easy to hose down.
- Cats require plenty of social contact with owners. You can provide access to the house through a cat door (and tunnel if applicable).
- Each enclosure should have a scratching pole and provide cats with at least two platforms at different heights. The platforms should be connected by static (planks) or swinging walkways. Cats should also have climbing frames and an interesting visual outlook.
- In a group enclosure, a number of hiding and escape areas should be provided so cats can avoid aggression from other cats.
- The size of your enclosure depends on the number of cats you need to house and how well they get on. The floor area of an enclosure must be at least 2 square metres for each cat, with a minimum height of 2 metres, plus tunnels and auxiliary enclosures. These dimensions are based on the presumption that cats will also have regular access to the house.
A basic walk in unit is an essential. It should incorporate a:
- weatherproof sleeping compartment
- raised bed or hammock
- specific feeding area
- separate bowl for each cat.
This basic unit can be linked to one or a number of other enclosures through wire tunnels (see Figure 10 for an example of a finished free standing cat enclosure). The enclosures are made from an open welded mesh and can be used to keep the litter tray well away from the main eating and sleeping area.
Base unit
The base unit is constructed around a simple steel frame welded from square section tubing, and includes a walk in door for cleaning. The unit is clad with a combination of steel sheeting and wire netting.
See Figure 10 for an example of a finished free standing cat enclosure, including a base unit. The frame can be welded, which is easy to learn so if you can borrow a welder and get some instruction, spend time with scrap steel and practice. The easiest welding position for a beginner is to weld a horizontal joint, so it is a good idea to turn the work where possible to present a flat welding position.
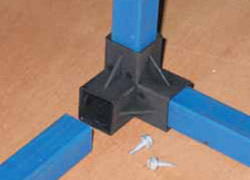
Figure 1
Tools required
- cordless drill and bits
- Tec screw driver bit wheels
- pop rivet gun
- roofing square
- tape measure
- tin snips
- handsaw
- pliers
- 8mm masonry bit
- F clamps with plastic feet
- angle grinder with cut off and grinding
- safety goggles
- leather gloves
- welder (note that welding is optional)
- welding magnets
- welding hammer
- welding mask
- bolt cutters (450mm minimum length).
Material checklist
- 25 × 25mm square tubing, primed
- 25 × 25mm galvanised mesh
- scrap steel offcuts
- 50 × 50mm galvanised mesh
- Trimdec capping
- Tec screws and washers
- hinges
- latch
- tie wire
- primer and paint
- 8mm Dyna-bolt
- fence sheeting.
Construction
Step 1: Design
Read through the step-by-step instructions to familiarise yourself with the component units and the construction techniques and then establish the number and type of units that you require.
Go outside and decide on your preferred layout, marking it out with pegs, paint or tape. See 'Cat enclosure attached to an existing structure' section, Construction Step 1 for an example of a stringline set out.
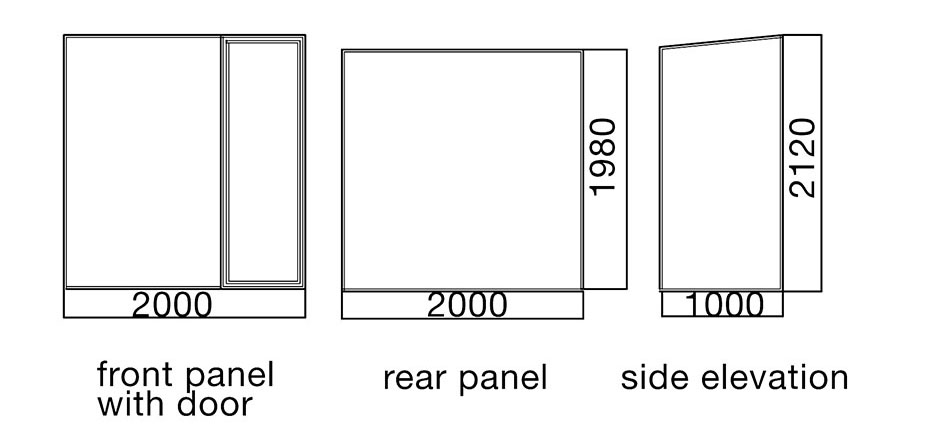
Figure 2
Step 2: Prepare a cutting list
Working from your plan, prepare a materials and cutting list. Here is a sample-cutting list that has been taken from the drawing of the basic unit in Figure 2 which constructs an approximate 1 × 2 metre enclosure (which is the minimum size per cat — see 'Design Considerations' for details).
Prepare a similar cutting list from your plan.
Material 25×25mm tubing | Quantity | Size |
---|---|---|
Front panel uprights | 2 | 2050mm |
Door jamb | 1 | 2050mm |
Top and bottom rails | 2 | 2000mm |
Door | 2 | 19800mm |
Door | 2 | 680mm |
Rear panel uprights | 2 | 1900mm |
Top and bottom rails | 2 | 2000mm |
Roof support | 2 | 1060mm |
Bottom side rails | 2 | 1000mm |
Cut 25 × 25mm square tubing to length with angle grinder and cut off wheel ensuring that all cuts are square. Alternatively, your steel supplier can provide tubing cut to size and give you clean accurate burr free joints that are easy to weld.
Step 3: Assembling the steel frame
Welding
- Lay out the components for the front frame on a flat surface and tack weld the joints.
- Check the joints are square with a roofing square and finish the welds.
- Make up a door to suit the opening.
- Lay the door in position and fix to the doorframe by welding hinges and latch.
- Using this finished frame as a jig, lay out the back frame components on top and weld the joints. To join the front to the back it is best to enlist another pair of hands to hold everything in position.
- Weld the two bottom rails in position, gently tip the structure on its side and weld the roof joints, continually checking for square as you go.
- Now weld in the internal brackets for fixing points for beds, climbing ramps, feed or water stations. The structure may appear a little unstable at this stage, but there is no need to worry, as the cladding will provide adequate bracing when fixed.
- Check all joints and grind off any excess welds and burrs.
- Prime the joints with metal primer and then finish with a good exterior paint.
Welding tips
- Have water handy when welding to cool the welds.
- A welding magnet can be used to hold components in place when tack welding joints.
- If you are using an arc welder then pick off the slag from the welded joint as you go and re weld where necessary.
- If you live in a coastal area, specify a salt resistant sheet steel cladding.
Figure 3
When using prefabricated joiners, see Figure 1, follow the same construction order, fixing each joint as you go. Use self drilling Tec screws or bolts to attach the door hinges, latch and fittings and finish the frame with a good quality exterior paint.
Step 4: Installation
If fixing on a concrete base, first check for square by measuring corner to corner. See 'Cat enclosure attached to an existing structure' section, Construction Step 1 for an example of a stringline set out. Fix the bottom rails with 8mm Dyna-Bolt. See Figure 3.
Where there is no concrete base, fix the frame directly to the ground with tent pegs driven through holes drilled in the bottom rail.
Step 5: Door
If you find that the finished door lacks rigidity then clad the bottom section with metal cladding which will act as a brace. The hinges and latch are fitted to the frame on the outside with welds or self drilling Tec screws. See Figure 4. Give some thought to a childproof locking system.
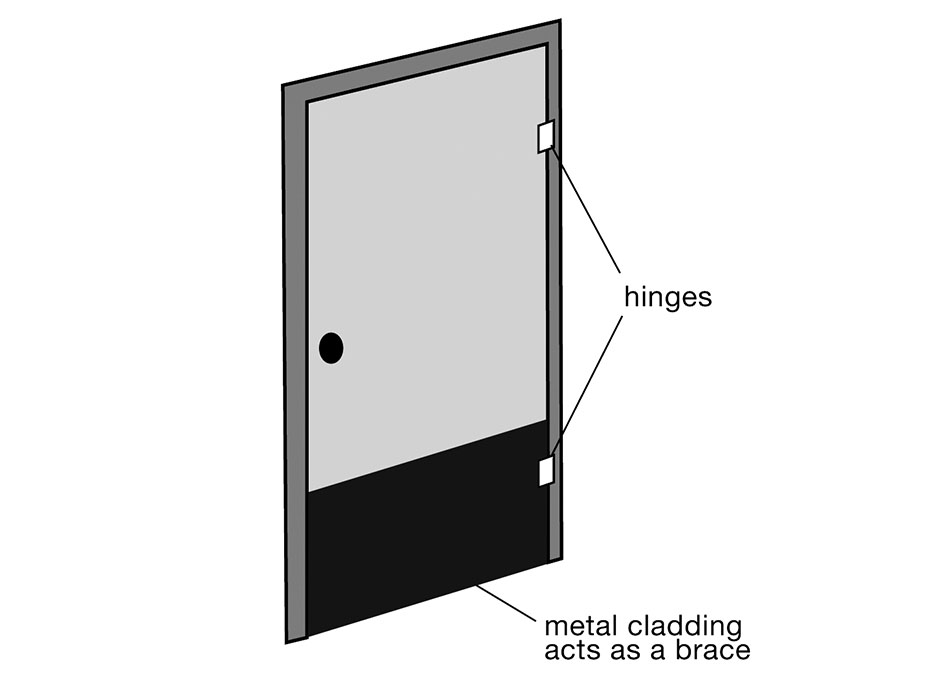
Figure 4
Step 6: Cladding
First establish the shelter requirements for your base unit and plan which areas will be covered with sheet steel and with wire mesh.
Mesh
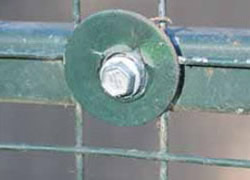
Figure 5
Sheeting
- Calculate the sheet sizes required, bearing in mind that the standard cover is 760mm per sheet. The material is available in a range of stock lengths that you can cut to size with an angle grinder and cut off wheel. The cladding is fixed with self-tapping Tec screws and a cordless drill.
- Fix the first panel along the upright steel corner frame and check that the frame is square and then clamp the panel to the horizontal rails.
- Check again and then fix these edges with the Tec screws.
- Continue fixing around the frame until completed. (See Figure 6.)
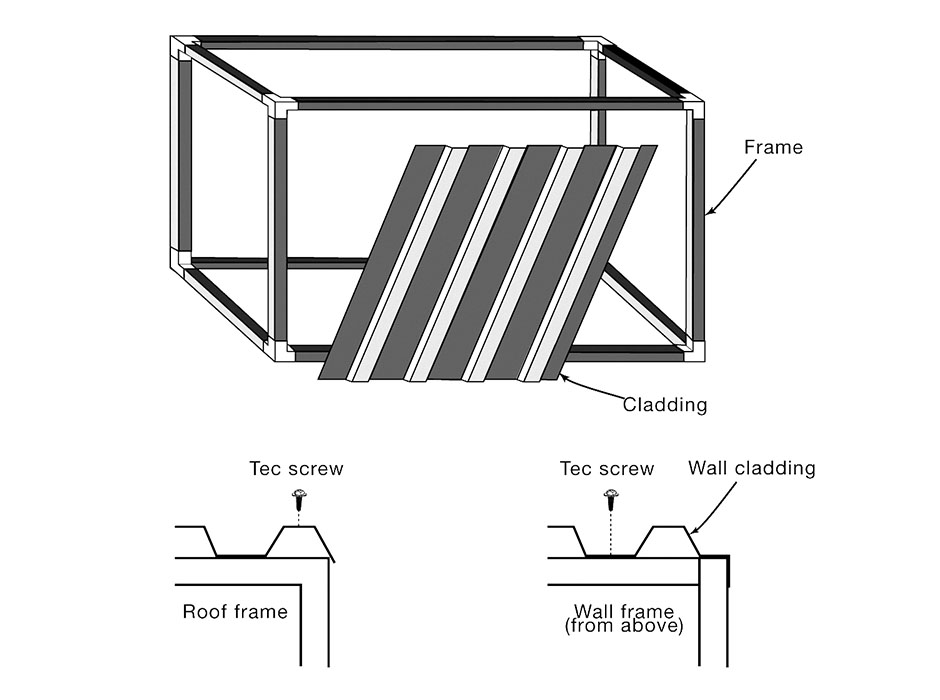
Figure 6
Roof
- Measure the roof opening from corner to corner to check for square and fix the roof panels across the narrow width. When affixing roof sheets, tec screws must be used on the high points of ridges in the roof cladding.
- Now cover the exposed edges of the roof cladding with 'U' section steel capping, using self drilling roofing Tec screws. See Figure 7. However it should be noted that larger enclosures may require extra roof support.
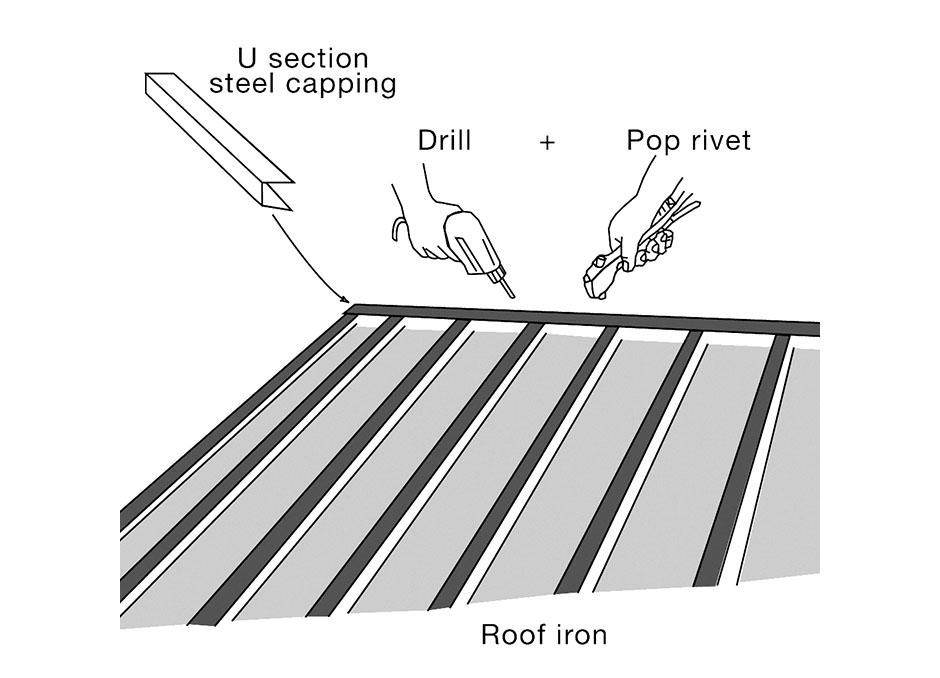
Figure 7
Auxiliary mesh enclosures
These freestanding units are constructed from 50 × 50mm galvanised welded mesh, wired together with galvanised tie wire. The size and shape of each enclosure will depend on your requirements and also the stock sizes of mesh that is available from your supplier. Common sheet sizes are 2400 × 1200mm, 2000 × 1200mm and 3000 × 2400mm.
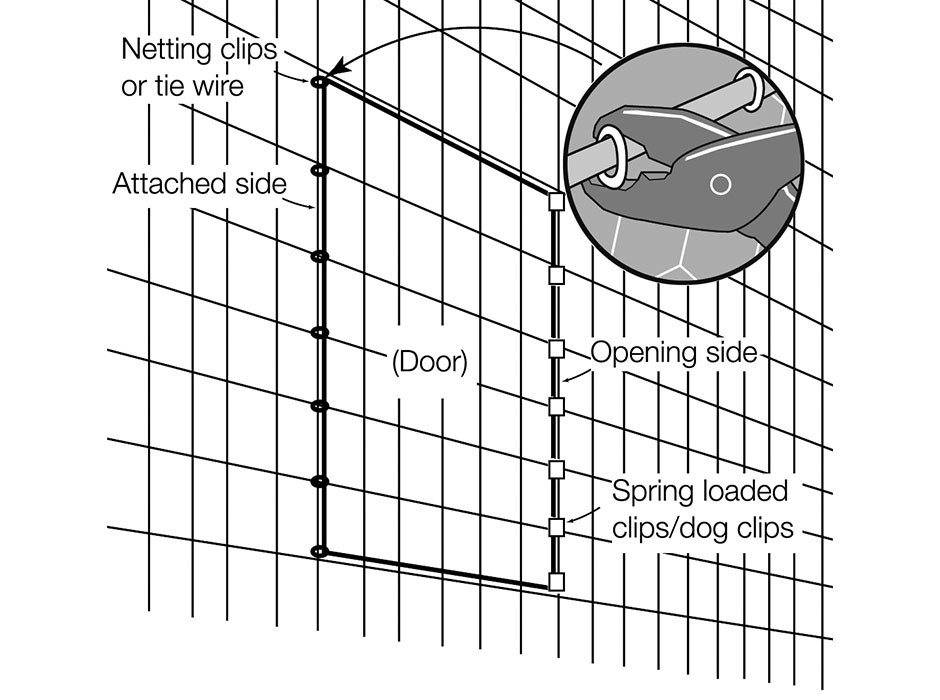
Figure 8
See Figure 9 for an example of a finished free standing cat enclosure, including an auxiliary unit.
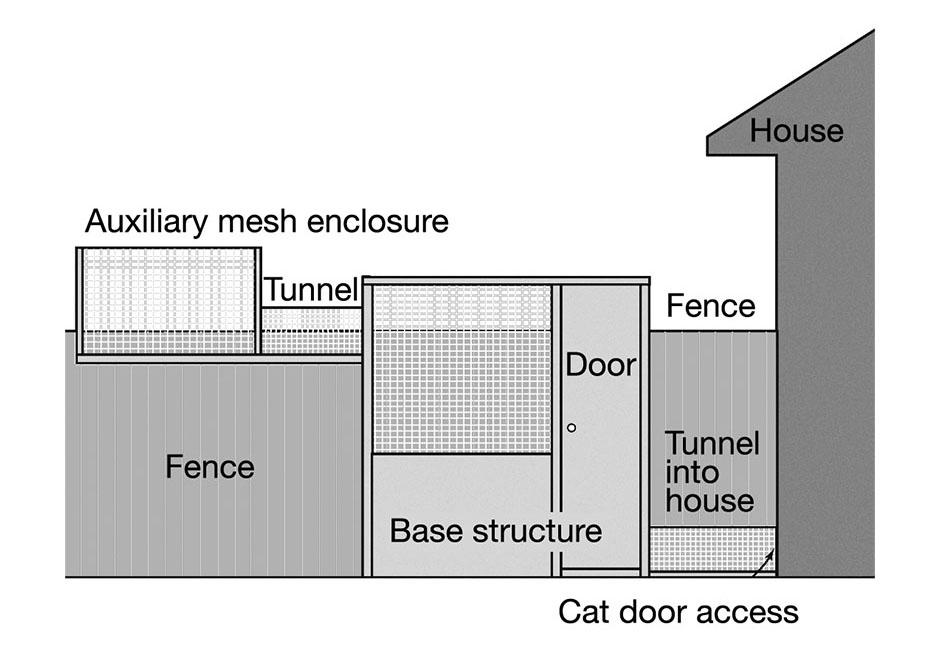
Figure 9
Tools required for the job
- tape measure
- F clamps
- bolt cutters 450mm
- roofing square
- angle grinder
- hammer
- pliers with wire cutter
Materials list
- 50 × 50 galvanised weldmesh
- tent pegs or masonry plugs
- hardwood post 50 × 50mm
- galvanised tie wire
- dog clips
Step 1: Design and construction
- Visit your steel supplier and obtain a list of stock sizes that are available and design the modules around these stock sizes to minimise off cuts.
- Cut the mesh with the angle grinder or bolt cutters and grind off sharp protrusions.
- Tie the panels together with tie wire. As cats do not dig deep enough to escape there is no need for a floor panel, and the enclosure can be held in place with either tent pegs or masonry plugs.
- For a door simply cut a small opening and cover with an oversize piece of mesh hinged on one side with tie wire or netting clips.
- The hinged door (which should open inwards) can be latched closed, with spring loaded clips (like dog clips). See Figure 8. Depending on how flexible the mesh is, you may need to secure the door with multiple clips to prevent the cat from squeezing through gaps. If you prefer, the entire lid panel can be hinged to allow easy access.
Step 2: Fittings
Each enclosure should provide a hardwood scratching pole, which can be fixed to an internal wall with tie wire.
The enclosure also requires at least two levels of platforms that are joined by a climbing plank (platforms can either be supported by a stand or wired to the structure).
Step 3: Access tunnels
Note: Figure 9 shows the basic bullring structure prior to the addition of other features (platforms, climbing planks, scratching posts, beds etc) as described in the text)
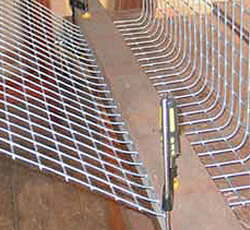
Figure 10
These tunnels are made by folding a 900mm wide length of weldmesh and anchoring it to the ground. Either bend the 900mm wide weldmesh over in an arch and fasten it across the bottom with tie wire, or bend two right angles with the aid of a jig made from 2 lengths of hardwood and clamps. See Figure 10.
If a tunnel is to be suspended off the ground, the floor is made from 300mm wide lengths of steel cladding that is wired to the bottom of the tunnel with tie wire.
The tunnels are wired on to the component units and all protruding wire ends are folded back out of harm's way.
To give your cat an entertainment centre, put a birdbath within view just outside the enclosure. It doesn't seem to worry the birds and will provide your cat with hours of entertainment.