Fertigation
Fertigation, also called nutrigation, is the application of soluble fertilisers and micronutrients to crops through an irrigation system. Drip irrigation is highly suited for fertigation. Fertigation is generally used to supply the crop’s nitrogen, phosphorus, potassium, calcium, and magnesium needs. Soluble and liquid forms of various micronutrients are also now suitable for use in fertigation. Care must be taken to avoid incompatibility issues when using these products.
Intensive fertigation management involves injecting nutrients using computer-controlled equipment and multiple tanks. More information is available in Fertigation Equipment for use in Orchards on the NSW Department of Primary Industries website.
Advantages
- High uptake efficiencies because fertiliser is applied directly to the root zone. Less volatilisation.
- Fertiliser applications can be timed to crop requirements and physiological stages, leading to more control over shoot growth, yield, fruit quality and water use efficiency.
- Losses from rainfall leaching minimised by splitting fertiliser applications over several irrigations.
- Reduced labour, fuel, and machinery costs associated with manually applying fertiliser. Less traffic also results in reduced compaction and improved soil structure and better soil health.
- Fertigation equipment can be automated to allow accurate control of nutrient delivery. If appropriate fittings exist, the same equipment can also be used to help prevent emitter blockages by allowing the injection of hydrogen peroxide, chlorine, or acid.
Disadvantages
- The uniformity of fertiliser application depends on the uniformity of the irrigation system. The irrigation system must be designed and maintained correctly to ensure even water and fertiliser application over the irrigated area. System uniformity should be regularly checked.
- Restricted to using soluble or liquid products.
- Corrosion can occur if the system is not made of resistant fittings, and also flushed and cleaned regularly.
- Soil can become acidic with long-term use of ammonium-based nitrogenous fertilisers.
- Risk of blockages if incompatible fertiliser mixes are used. (Phosphorus-containing fertilisers mixed with calcium-containing fertilisers is the most common example).
Fertiliser injection should be long enough to ensure that equal amounts of fertiliser reach all trees in the area being irrigated, making sure injection is not so late in the irrigation cycle that nutrients remain in pipelines when the irrigation cycle stops. An understanding of travel times is important.
Units of concentration
Nutrient concentrations are normally expressed as parts per million (ppm) in the irrigation water. In standard metric units, 1 ppm is equivalent to the following:
- 1 microgram (μg) of nutrient per g of product (solid) or per mL of product (liquid)
- 1 milligram (mg) of nutrient per litre (L)
- 1 gram (g) of the actual nutrient per 1,000 litres (1 cubic metre or 1 m3) of water
- 1 kg per megalitre (ML).
Using the proportion or percentage of nutrient in a particular fertiliser, the concentration of fertiliser can be calculated. For example, if using urea (46% nitrogen) as a nitrogen source:
Solubility and how much to apply?
The amount of nutrient to apply to an orchard is normally defined in terms of kg/ha. Calculations need to be made back from kg/ha to estimate how much soluble fertiliser to supply for a given area. These calculations must consider the solubility of the fertiliser in the solution (see Table 1), the size of the tank and the length of the injection period. Solubility is important to consider when fertigating as all fertilisers have a different level of solubility. Solubility is also influenced by temperature.
For example, using urea (46% nitrogen) as the nitrogen source:
Total amount of urea to be supplied
Volume of water need to dissolve urea
Solubility of urea in water at 10°C = 30 kg/100 L from Table 1 (0.3 kg/L)
This volume is much less than the volume of the holding tank (500 L), so this amount of urea can be safely dissolved in a full tank.
Urea is very soluble. In the example above, approximately 100 kg of urea can be dissolved in approximately 350 L water (a ratio of 1:3.5). Other fertilisers are not so soluble and higher ratios are required. As a general rule for all fertiliser products, dissolve 100 kg fertiliser per 500 L of water (a ratio of 1:5 or 20%).
A 1:5 ratio can appear very conservative, and the temptation might be to add a greater amount of fertiliser to be dissolved, but nitrogen fertilisers cool the mixture when dissolving, lowering the solution temperature and solubility. Conservative mixing ratios should always be used, and recommendations relating to 10oC (See Table 1 below) regardless of ambient temperature should generally apply.
In the example above, if the fertiliser is to be supplied in one hour towards the end of the irrigation cycle, the fertigation pump must be able to inject at least 362.3 L/h to leave enough time afterwards to flush all fertiliser from the system.
Injection timing
Drip irrigation requires frequent irrigation, therefore irrigation events specifically for fertigation are often not possible.
If fertiliser is injected during a typical irrigation to meet the crop’s water requirements, the general view is that the fertiliser should be injected as late as possible in the irrigation event, but still leaving enough time to flush the system clean following the injection.
Injecting late in the irrigation event leaves the fertiliser in the upper part of the root zone so that future irrigations, if managed correctly, will not push unused fertiliser past the root zone, leaving it available to the plant for longer.
The term ‘advance time’ is the time taken for water to reach the furthest point of the system. It needs to be considered when determining the time needed to clean the system of fertiliser following injection.
Advance time is the time period when the system is fully pressurised, and not the time taken to initially fill the system. Advance time can be determined with knowledge of pipe lengths and diameters.
Excessive irrigations should not be applied after fertigation. Many irrigators prefer to apply around 75% of their normal irrigation following fertigation to ensure that nutrient loss is kept to a minimum.
Irrigation scheduling becomes very important however, to ensure that the tree’s water requirements are still met. Fertigation irrigations and leaching irrigations should be separate events, applied at different stages.
Growers who adopt intensive fertigation practices are continuously injecting fertiliser during most - if not all - drip irrigation events throughout the season.
This can create logistical issues if needing to clean the system with chlorine or hydrogen peroxide. Specific cleaning events need to be scheduled around fertigation events in order to avoid system precipitation problems.
Suitable fertilisers
There are numerous inorganic fertilisers specifically developed for fertigation (often termed ‘tech grade’). Many of these are now available in liquid form. Liquid forms often have a slightly lower nutrient concentration due to solubility requirements.
Most commonly used (granular) fertilisers are also suitable for fertigation, as long as they are soluble and free of impurities.
They generally take longer to dissolve and can require agitation. Fertilisers should always be injected downstream of the filters. The composition and solubility of some popular fertilisers are listed in Table 1 below.
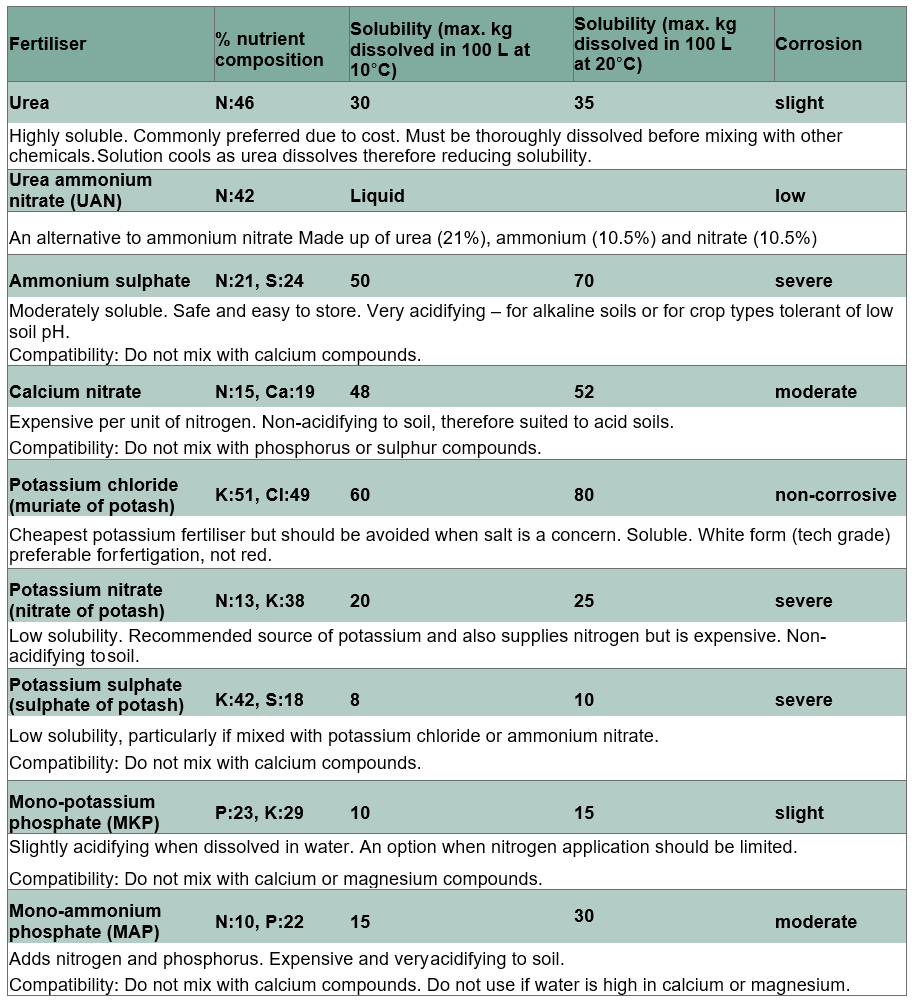
Table 1. Characteristics of various commercial fertilisers.
nitrogen (N), phosphorus (P), potassium (K), sulfur (S), calcium (Ca), chloride (Cl)
Solubility will vary for specific fertilisers. Different forms (granular compared to prilled) and additives, including insoluble residues, will vary between products, resulting in different solubility data. Seek manufacturers recommendations for specific advice.
Corrosion
Most fertilisers are corrosive to metal. It is important to select components that are resistant to corrosion. The more acidic the fertiliser, the greater risk of corrosion.
Incompatibility and precipitation
Some soluble fertilisers may not be suitable with others due to the formation of precipitants. These can settle at the bottom of the mixing tank or block filters and emitters if suspended. This problem most likely occurs when calcium-containing fertilisers mix with phosphate or sulfate fertilisers. Incompatibility charts can help understand compatibility.
To avoid issues, separate injection of phosphorus/sulfur fertilisers from calcium fertilisers. Rinse equipment and irrigation system between injections. Alternatively, use traditional broadcast/banding methods. Many irrigators with intensive fertigation use separate injection tanks.
Precipitation can also result from water quality: hard water with calcium or groundwater with dissolved iron reacting with phosphate or sulfate fertilisers.
For product compatibility, perform a simple jar test. Mix irrigation water with fertilisers (at the correct injection ratio, e.g., 1:5). Shake mixture well to check for dissolution. If solution is not mixing, avoid injection. Cloudiness, sedimentation, or coagulation after 24 hours also indicates unsuitable fertigation mix.
Compatibility information is often unavailable from manufacturers or suppliers. This can be due to insufficient research into all product combinations possible, over a range of water quality possibilities.
Organic products and drip irrigation
Organic nutrients are becoming popular for use with many horticultural crops. Products include bio-stimulants, seaweed, kelp extracts, amino, humic, acetic and citric acids. It should be noted that many of these products are low in solubility and can result in sedimentation and system clogging. In addition, how these products behave when combined with certain water sources, or standard inorganic fertilisers (N, K or Ca), is unknown but in many cases has resulted in unexpected system clogging.
Long term effects on components such as emitter diaphragms are also unknown, although new diaphragm materials are being developed to make them more resistant to a wider range of pH and chemical products.
System flushing after using these products is particularly important. Ability to clean sediment deposited at the bottom of tanks is also necessary. An industry specialist or supplier should be consulted if there is any doubt whether a particular product should be injected through a drip irrigation system.
Soil acidification
Soil acidification has been reported in orchards established on alkaline soils. It is a potential problem with the long-term use of ammonium-based fertilisers. This risk is greater when fertigating with drip irrigation as the total nutrient requirement of the plant is supplied to a relatively small volume of soil.
Soil acidification can occur if excessive nutrient leaching occurs due to poor irrigation management. When nitrogen is added to soil, nitrification (the conversion of ammonium to nitrate by soil bacteria) initially acidifies soil, but nitrate uptake by plant roots corrects that effect to some extent. If the nitrate produced from ammonium by soil bacteria is leached from the root zone by excess irrigation or rainfall before the plant can take it up, the soil remains acidic.
The risk of soil acidification is much greater on acid soils than alkaline. It is important to know the soil pH when choosing a fertiliser. Alkaline fertilisers such as calcium nitrate should form a significant part of the total nitrogen supply on acid soils.
The wetted volume of soil should be monitored to pick up any changes in pH, particularly if the soil was acidic when the fertigation program began. Preventing soil acidification is easier than correcting subsoil acidification caused using ammonium-based fertilisers.
Fertigation equipment
There are 2 basic injection methods:
- Pressure differential injection, using either pressure tanks or venturi systems; and
- Injection, using either electric or hydraulic pumps.
These methods can be used in standard, traditional ways or incorporated into intensive fertigation systems.
Pressure differential injection
A pressure differential injection system is based on the principle of a pressure differential being created by a valve, pressure regulation, elbows or pipe friction in the mainline, forcing water through a bypass pipe into a pressure tank and out again, carrying a varying amount of dissolved fertiliser. Two common methods are pressure tanks and venturi systems.
This system uses a pressurised tank (Figure 1) containing fertiliser with a proportion of the irrigation water being diverted through the tank (Figure 2) dissolving the solid fertilisers and then injecting this into the irrigation system. Tanks can be installed in the field, allowing fertiliser to be applied to specific patches, and avoiding distribution through long mainlines.
Advantages
- Simple and inexpensive to install and operate
- Easy to maintain
- Easy to alter the type of fertiliser to be injected
- Power source not required.
Disadvantages
- The concentration of fertiliser solution decreases over the injection period, leading to poor nutrient placement
- Requires a loss in pressure in irrigation mainline/ submain
- Proportional fertigation is not practical on large scale systems
- Unsuitable for automation
- Tank and piping must be sealed and able to withstand mainline pressure
- Liquids are preferred and give best results due to a lack of agitation for powder formulations
- Tank size limits this method to relatively small irrigation systems.
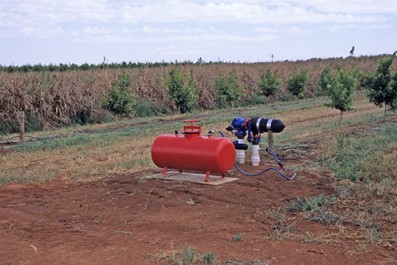
Figure 1. Pressure tank installed in the field
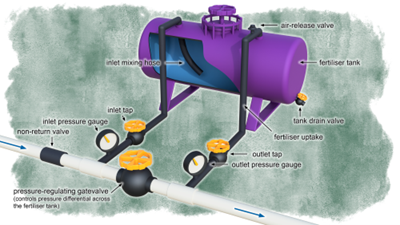
Figure 2. Schematic diagram of pressure tank system.
Pressure differential can also be used to operate a basic venturi injector, either as a bypass or in-line (Figure 3). A venturi injector creates a vacuum that sucks dissolved fertiliser into the irrigation system (Figure 4). These units require a pressure loss that must be provided by the irrigation pump or a small booster pump.
Advantages
- Simple to install, operate and maintain
- Suitable for proportional fertigation
- Injection rate adjustable
- Injection rates can be controlled with a metering valve.
Disadvantages
- Requires pressure loss in mainline (can be 30%) or a booster pump
- Unsuitable for larger properties
- Quantitative fertigation is difficult for basic systems. Advanced venturi systems allow larger flow rates and proportional injection (Figure 5 below).
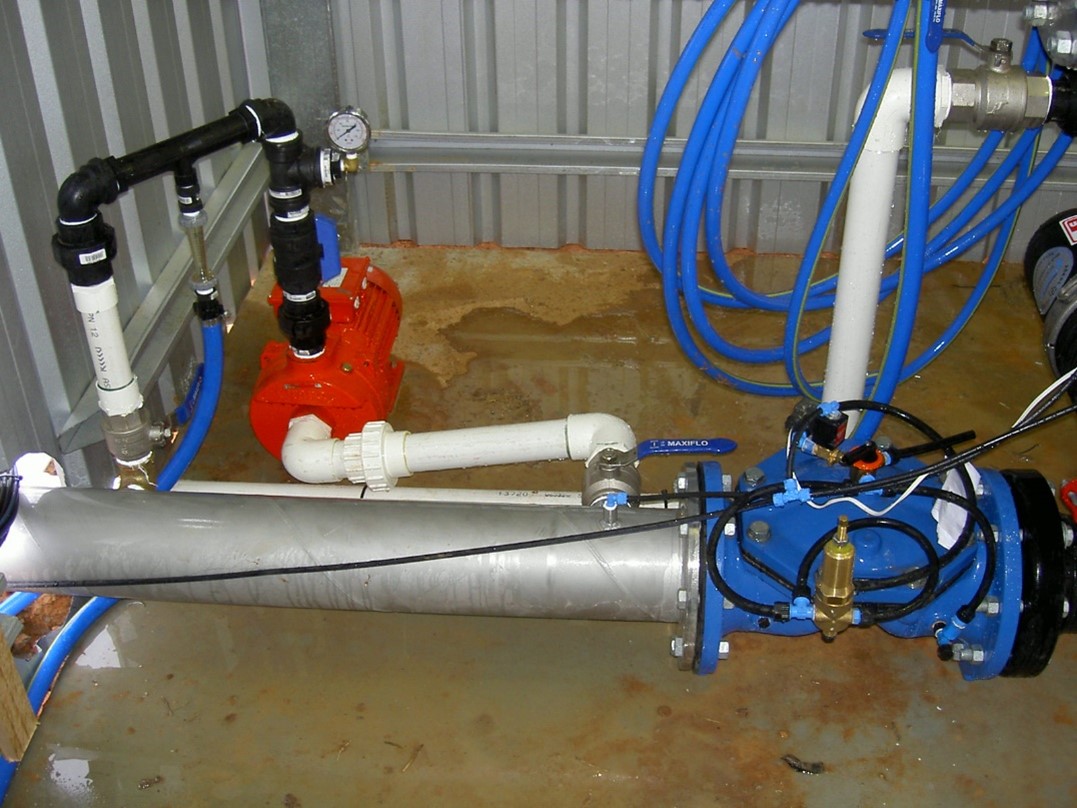
Figure 3. Venturi system. Photo: Peter Henry
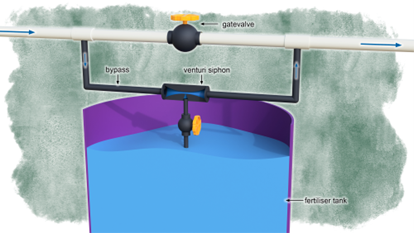
Figure 4. Schematic diagram of a bypass and gate valve venturi method; one of several arrangements that can be installed using a venturi injector.
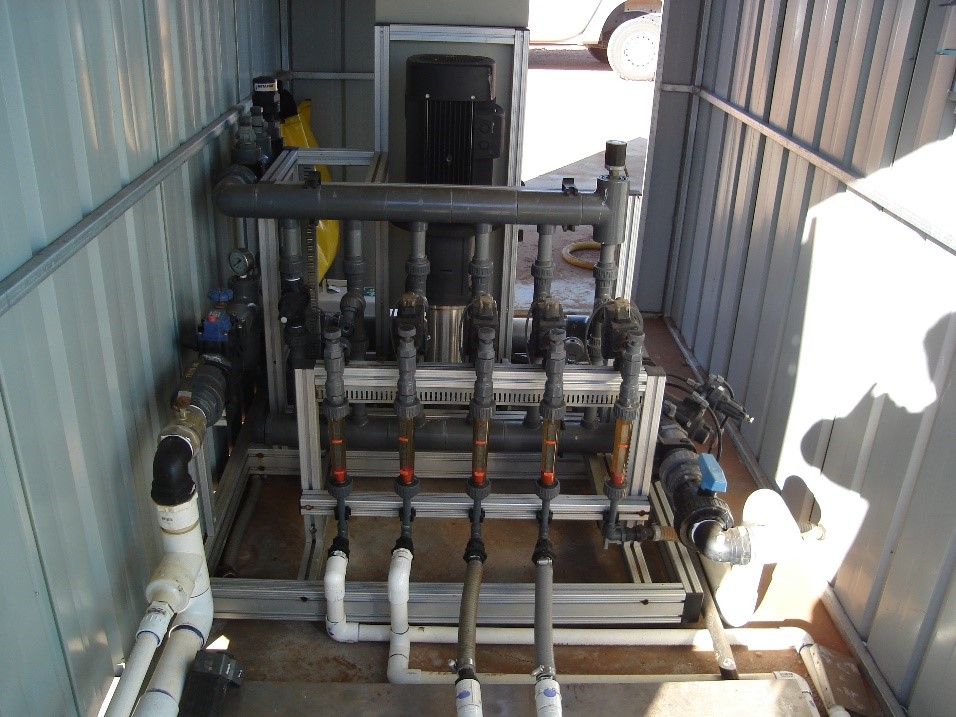
Figure 5. Advanced venturi system. Photo: Peter Henry
Injection pumps
Injection energy can be provided by electric motors, impeller-driven power units and water-driven hydraulic motors.
Electric injection pumps (Figure 6) are either centrifugal, piston or diaphragm. They create a higher than mainline pressure to force fertiliser into the system. This method can be very accurate. Pumps are generally not simple in design and can include several moving parts, so wear and breakdown are more likely.
Advantages
- Simple to install, operate and maintain
- Suitable for either proportional or quantitative fertigation
- Injection rate is adjustable
- No pressure loss in mainline
- Suitable for automation.
- Electric power source required
- Pump must develop minimum mainline pressure to operate.
Disadvantages
- Electric power source required
- Pump must develop minimum mainline pressure to operate.
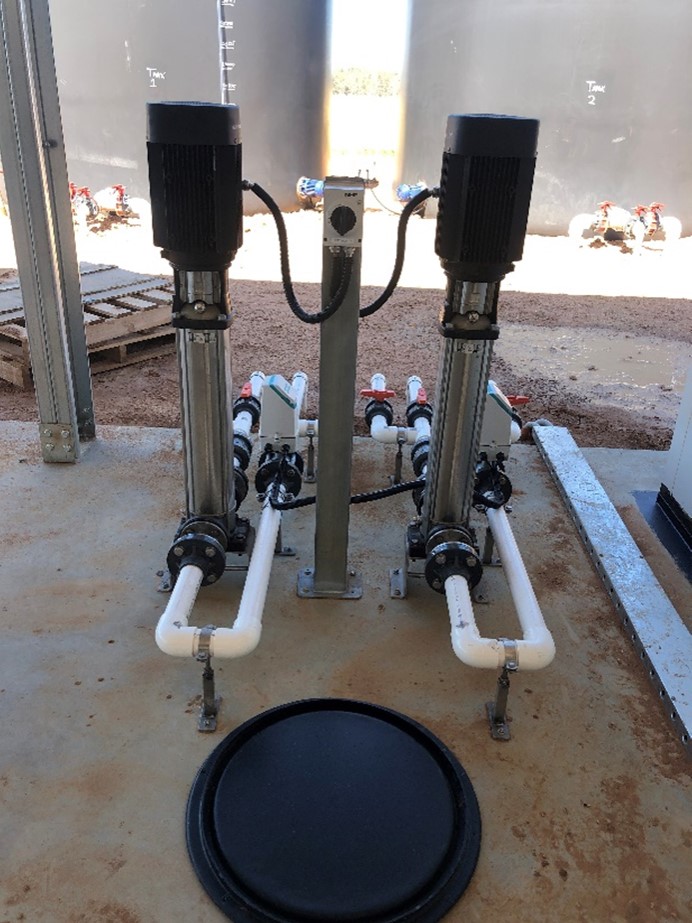
Figure 6. Electric injection pump. Photo: Peter Henry
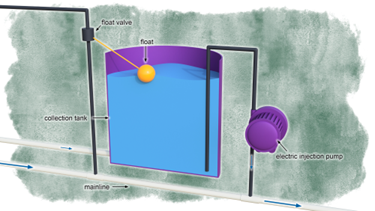
Figure 7. Schematic diagram of electric injection pump.
Hydraulic injection pumps are either piston-activated or diaphragm-activated. The pump’s maximum rate of injection is proportional to either the mainline flow for inline installations, or pressure-differential (PD) when installed on a bypass. For units run on mainline pressure, the water used to drive the pump is run to waste at a rate of 2 to 3 litres for every litre of fertiliser injected.
Advantages
- Electric power source not required
- Portable
- Simple to install, operate and maintain
- Suitable for either proportional or quantitative fertigation
- Injection rate is adjustable
- Units utilising mainline pressure do not induce mainline pressure loss
- Highly suitable for automation, low labour requirement.
- Regular maintenance required
- Pumps require a minimum line pressure
- Suitable for smaller systems only
- Can create wastewater which requires disposal.
Disadvantages
- Regular maintenance required
- Pumps require a minimum line pressure
- Suitable for smaller systems only
- Can create wastewater which requires disposal.
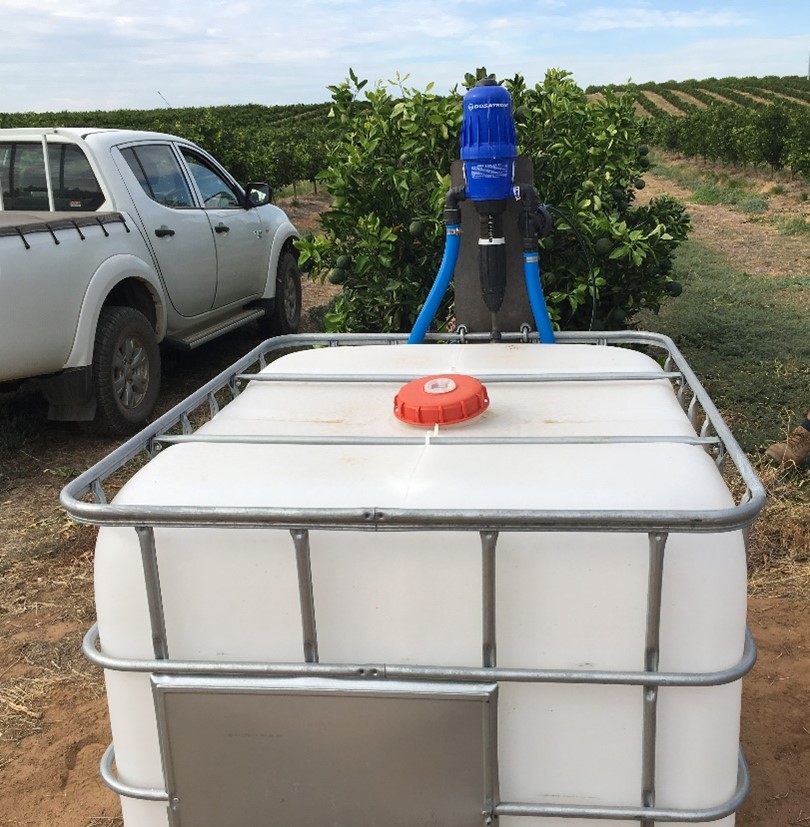
Figure 8. Portable PD hydraulic injection pump. Photo: Peter Henry
Multiple tanks
Intensive irrigation and fertigation management systems use computer-controlled, multi- tank systems with a variety of injection methods such as positive displacement pumps or venturi type systems. A computer controls the injection rate and monitors the mainline flow rate to provide proportional injection. Multiple tanks are commonly used in these systems (Figure 9).
Usually, the first tank contains a nitrogen, phosphorus, potassium, and magnesium nutrient solution, the second tank a calcium and iron nutrient solution and the third an acid solution to reduce the pH of the water to approximately 6.5. The pH of the irrigation water is buffered to 6.5 to reduce the incidence of precipitation of nutrients and to increase the ability of the roots to take up nutrients.
Various designs and layouts are available to suit large and small-scale orchards.
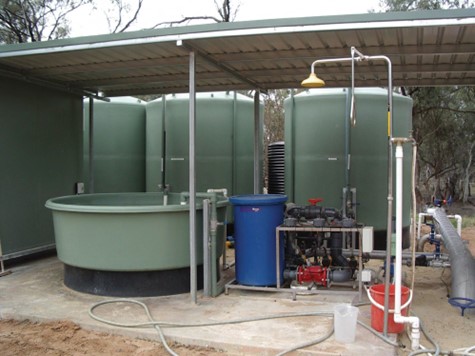
Figure 9. Advanced three-tank computer-controlled proportional injection fertigation system. In the foreground is a mixing tank to dissolve and mix fertilisers, with three main nutrient tanks in the background.
Monitoring pH and EC
To optimise fertiliser uptake and reduce the likelihood of chemical precipitation, some irrigators choose to maintain the pH of the solution (usually pH 5.5–7 depending on the crop and situation). Probes (Figure 10) are used to monitor pH and adjust injection rates accordingly. pH probes require regular re-calibration and periodic replacement.
Some managers practicing intensive fertigation practices may also be interested in monitoring electrical conductivity (EC) to avoid injecting a solution greater than the upper salinity limit that can be tolerated by the crop being fertigated. This can be important if intensively fertigating sensitive crops or at sensitive growth stages. Probes are also available for monitoring EC.
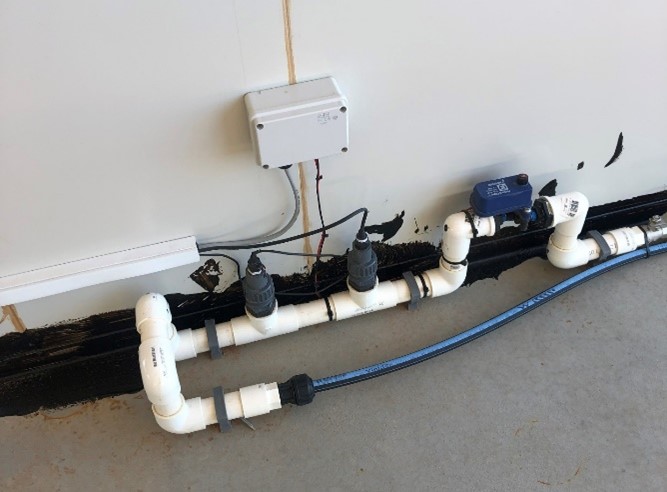
Figure 10. pH and EC probe. Photo: Peter Henry
Which system suits the situation?
Several factors will influence the choice of fertigation system. Aspects to consider include management style, skill level, farm size, farm layout and cash flow. Several scenarios are considered below:
- If no power is available at the site, options are limited to a pressure tank or hydraulic injection system
- For simple, small properties, a pressure tank system is suitable
- For greater accuracy, an electric injection system with a flow or totaliser meter is often recommended
- For larger systems, injection at the valve rather than through the mainline might be preferred. In this situation, a pressure tank, hydraulic pump, or generator-driven electric pump would be suitable.
Fertiliser tanks and piping
In any system where tanks and pipes are connected to the irrigation pumping system, care should be taken to ensure the equipment is able to withstand the pump discharge pressure.
Care is also necessary to ensure the fertiliser chemicals will not corrode the tank and pipes by electrolysis between dissimilar metals. Tanks, fertiliser pumps and filters should be located so that if spillage occurs, it can be washed away without corroding other equipment, such as shed framework or panelling.
Tanks should be designed to a maximum height of approximately one metre so that it is safe and practical to manually lift a 40-kilogram bag of fertiliser, rest it on the lid and empty into the tank. Taller tanks might require a raised platform.
Any risks to health and safety need to be assessed. Chemical users must ensure their own safety and be aware of community concerns about how chemicals might affect human health and the environment. See Working with chemicals.
Procedures
Before fertigation, it is crucial to thoroughly dissolve and mix fertilisers. Insufficient mixing can lead to uneven fertiliser concentration during irrigation, while incomplete dissolving may cause blockages to filters or emitters. You can find the solubility of common fertilisers in Table 1 above.
Different fertilisers require different amounts of water to dissolve, and small ratios can be used for highly soluble fertilisers (for example, urea). As a general recommendation, a ratio of 100 kilograms of fertiliser per 500 L of water (1:5 or 20%) is advised. It is important to design the tank size for each system accordingly. With adequate agitation, this ratio can usually be reduced to 1:3.
For every 25 kilograms of fertiliser added, expect a volume increase of approximately 15 L in the tank.
All fertiliser tanks require a suitable agitation system to dissolve fertilisers and prevent them from dropping out of suspension.
Refer to ‘Safety precautions’ below on using corrosive products.
Fertigation can be at a pre-set rate over the whole injection period, or it can be a proportional rate in which the injection rate varies with flow rate. The required dilution ratio depends on the concentration of the injected stock solution and the desired concentration of the nutrient at the emitter.
It is often an advantage to have an injector with a variable injection rate to allow for various chemicals and concentrations to be accommodated. Injection rates can be controlled by flow regulators, chemically resistant ball valves or by electronic or hydraulic control units.
The more sophisticated of the commercially available injector units can generally be adapted for automatic operation by fitting pulse transmitters. These pulse transmissions can be used to automatically dose the irrigation system with a precise quantity of fertiliser or chemical or to inject a set proportion of fertiliser or chemical in relation to the flow rate of the irrigation water.
The fertigation system should not be connected to any other water supply system for household, stock, or any other use. Suitable reflex valves and anti-siphoning valves should be installed where necessary to prevent back-flow or siphoning of water back into the fertiliser tank.
A check of the chemical concentration of the irrigation water in the system should be made to ensure correct mixing rates and to check the entire drip system is being evenly treated.
In large systems it can take much longer for the solution to reach the peripheral outlets than to reach those close to the injection unit. The injection process should, therefore, be timed so that all the nutrient solution is flushed through the system before the irrigation stops. A trial run using a dye instead of fertiliser solution will give some indication of the time required.
After fertigation, clean water should be flushed through the injector system to remove residual chemicals that can crystallise inside the unit. These chemicals can damage the injector and provide an ideal environment for the growth of micro-organisms, which can block outlets. Tanks should be designed with a sloping base to allow easy flushing and cleaning.
Safety precautions
Before using any corrosive product, the user should consult the manufacturer’s guidelines for transport, handling, storage, and use of the corrosive product and follow the appropriate occupational health and safety procedures.
- Read the label on containers and follow recommended directions on use, storage, handling and transport.
- Discuss with a manufacturer or retailer the details on recommended product use and dosage rates for purposes of cleaning or fertilising if necessary.
- Have reference to product physical and chemical properties (material safety data sheet).
- Obtain complete safety directions and have these displayed in a prominent location, particularly the emergency procedures.
- Obtain and follow the appropriate occupational health and safety procedures.
- Have the manufacturers and emergency services telephone numbers ready.
- Be sure of first aid procedures.
- Know the correct spillage treatments.
- Wear recommended protective clothing and body protection procedures when handling corrosive materials.
- Ensure proper ventilation when handling corrosive materials.
- Ensure that equipment and fittings (for example, drum taps) used for transferring a corrosive product from the storage container to injection tanks or other containers are resistant to chemical action.
- Ensure that all irrigation system components are manufactured to withstand the chemical action of corrosive products.
- Ensure corrosive products are injected into irrigation systems at the recommended rates.
- Check the compatibilities of products before mixing a corrosive product with other products; mixing incompatible materials can be dangerous.
- Add acid to water, not water to acid.
- Ensure the fertigation tank and injection equipment are thoroughly cleaned of any residual product after use and before the next operation. This will prevent the accidental combination of 2 products that are dangerous when mixed.
- Cool areas are preferred
- Place acids in a location separate from oxidising agents like chlorine
- Ensure products are kept secure.
Further Information
Contact Jeremy Giddings: jeremy.giddings@agriculture.vic.gov.au
Acknowledgments
- Peter Henry, Agronomist, Netafim Australia
- Ken Orr, Horticultural Consultant
- Tom Murphy, EE Muir & Sons, Mildura