Filtration for drip irrigation
Filtration is a crucial component of a successful drip irrigation system. While it may seem expensive at first, reliable filtration is essential for ensuring that drippers work properly and do not get blocked.
Two terms are used to describe filtration: mesh size and micron (µ).
Mesh size refers to the number of mesh spaces per square inch, with a higher number indicating smaller spaces and greater filtration. The standard mesh size for drip irrigation is 120 mesh or greater.
Micron (µ) refers to the particle size being filtered, with 1 mm equal to 1,000 micron.
The primary aim of any filtration unit is to remove particles that would block drippers, not necessarily to stop all particles below a certain size. For example, a mesh size of 120 will remove particles up to 130 µ, but particles as small as 2 µ (such as clay) can pass through the system if kept in suspension (see Table 1).
By ensuring reliable filtration, a well-designed drip irrigation system can function properly and provide efficient water delivery to crops.
Material | Particle size (µ) | Particle size (mm) | Mesh equivalent |
---|---|---|---|
Very coarse sand | 1,000–2,000 | 1.0–2.0 | 10–18 |
Coarse sand | 500–1,000 | 0.5–1.0 | 18–35 |
Medium sand | 250–500 | 0.25–0.5 | 35–60 |
Fine sand | 100–250 | 0.1–0.25 | 60–160 |
Very fine sand | 50–100 | 0.05–0.1 | 160–270 |
Silt | 2–50 | 0.002–0.05 | 270-400 |
Clay | <2 | <0.002 |
Table 1: Particle size in relation to mesh equivalent and micron (µ).
Source: Adapted from Netafim School of Irrigation 2004, Filtration module.
A balance is required between under- and over-filtration to ensure an acceptable flow rate is maintained, allowing suitable backflushing interval and volume, as well as controlling capital cost.
The smaller the emitter, the greater the risk of blocking. Therefore, drip irrigation systems have more stringent filtration requirements than other irrigation systems.
Minute particles that can move through the smallest outlet can, under some conditions, aggregate into larger particles and cause blockages. This has led to recommendations of very fine filtration for drip irrigation (generally micron size 1/6 –1/10 of the emitter outlet, compared to 1/3–1/6 for micro-jets).
The smallest pathway through most emitters is 500–1,000 µ (0.5–1.0 mm). This means drip systems generally require at least 120 mesh (130 µ).
Filters can be divided into three types: screen, media, and disc. Each filter type has advantages and disadvantages to suit particular situations.
Screen filters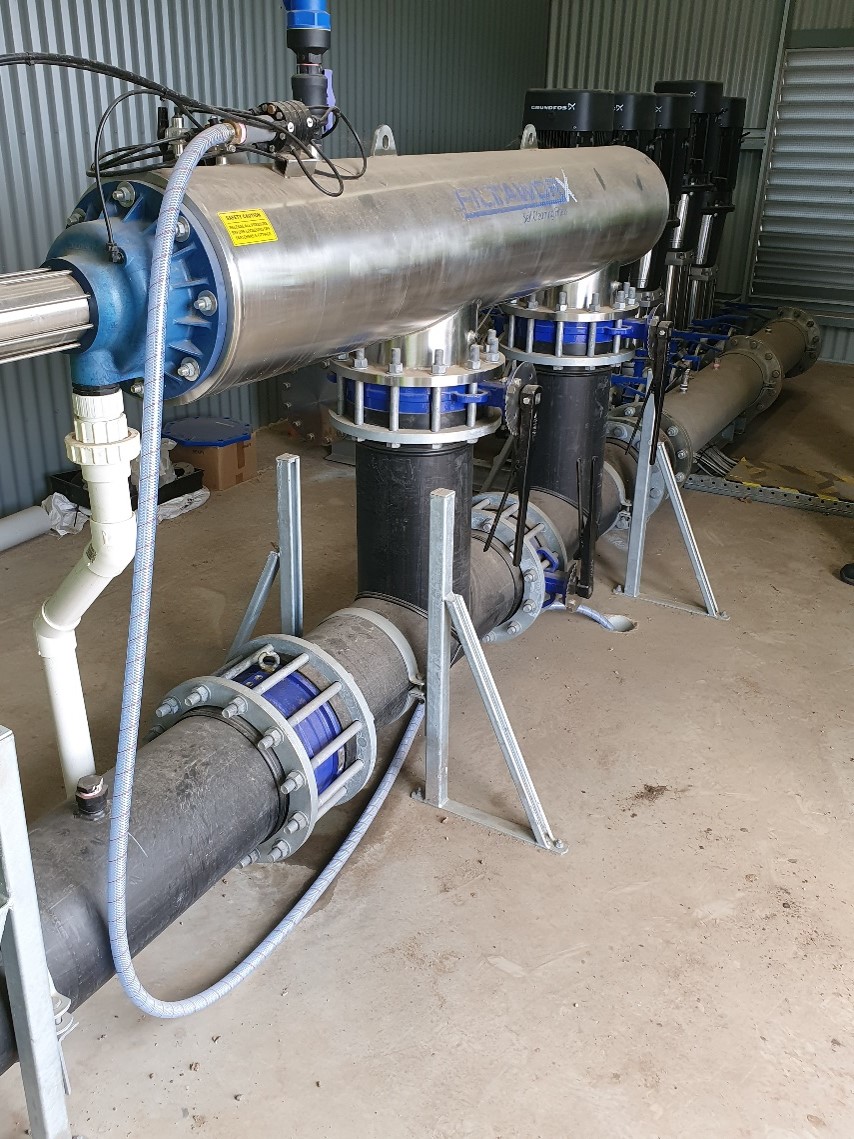
Figure 1: Typical screen filter. Photo: John Harvie
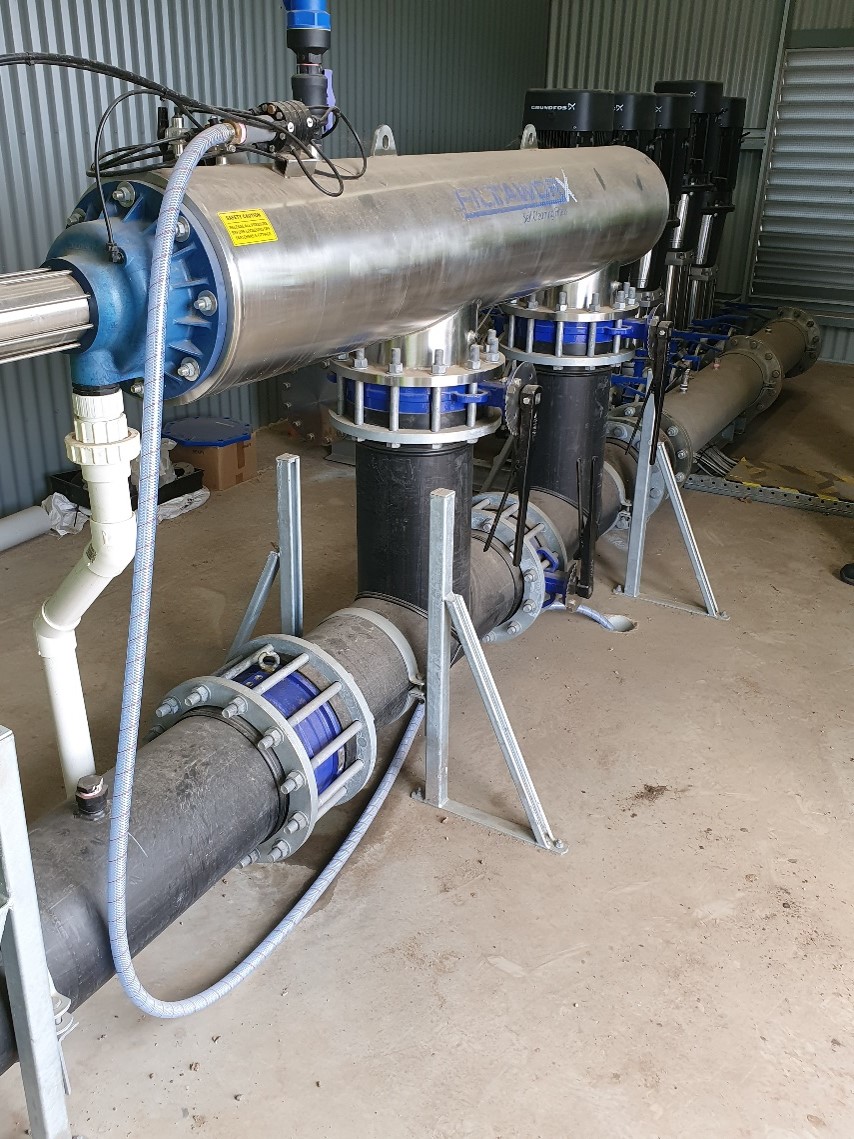
Figure 1: Typical screen filter. Photo: John Harvie
Screen filters (Figure 1) provide surface filtration, as opposed to depth filtration provided by media and disc filters. Screens are usually made of metal, plastic, or synthetic cloth, enclosed in a special housing. A coarse outer screen and fine inner screen usually exist to provide effective filtration. Improvements in their design and materials have increased their popularity.
Screen filters are referred to by their mesh size. Most screen filters can provide a range of mesh sizes suited to particular situations.
Backflushing screen filters: Automated suction scanners can clean screen filters without interrupting the filtration process. These mechanical ‘orifices’ rotate on the inside of the screen and suck water in the opposite direction to remove dirt build up. The self-cleaning process can be scheduled on a time interval or triggered by a pressure differential when debris accumulates on the inner screen.
Using screen filters in drip irrigation
Advantage
- Lower cost for a given flow
- Low head loss
- Smaller installation area (footprint) compared to media filters.
Disadvantages
- Screen filters only allow filtered water to pass through a single layer of mesh and are two-dimensional, compared with media and disc filters which have a third ‘depth’ filtration dimension. Greater attention to system maintenance might be required as a result. In some instances, a mesh of greater than 120 may be recommended.
- Generally, screen filters are used for drip systems where water quality is average to high.
- As only a single surface area of filter is available to trap solids, the amount of dirt that can be retained before a backflush is required is limited.
- A high-pressure differential may force organic matter through a screen filter.
Media filters
Media filters generally give the highest degree of filtration and are the most popular choice where dirty water is being used. These filters rely on the filtering action of sharp granite or silica, with an aggregate generally between 0.75–1.5 mm diameter.
Media filters trap a larger amount of very fine particles, such as silt, which makes them well suited to drip irrigation systems. Filtration is three-dimensional, with the total filter area being the product of the width, height, and depth of each tank (Figure 2). Multiple layers of filtering are possible, ensuring as many particles as possible are trapped. Examples of filter media (Table 2) indicate the particle size that can be removed by these filters. Filtration increases as media size reduces.
Media No. | Material | Average effective media size (mm) | Mesh equivalent |
---|---|---|---|
8 | Crushed granite | 1.5 | 100–140 |
11 | Crushed granite | 0.78 | 140–200 |
16 | Crushed silica | 0.66 | 140–200 |
Table 2: Examples of filter media
Backflushing media filters
Media filters are always backflushed in sequence, either at a set time interval or whenever the media becomes dirty enough to create a significant pressure differential between the tank inlet and outlet.
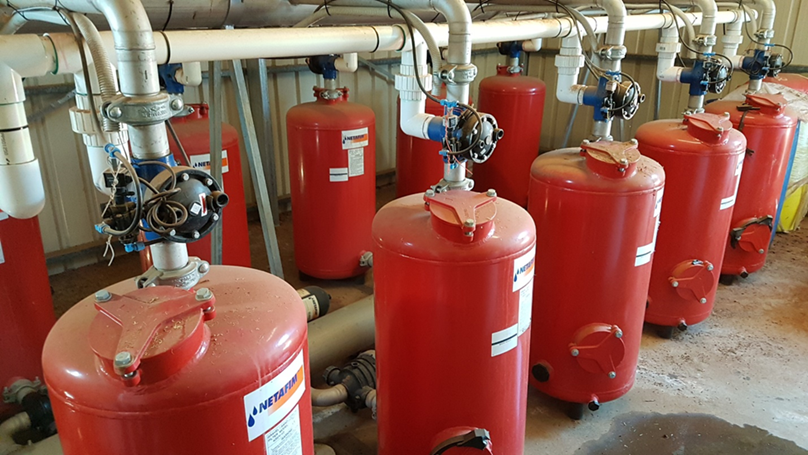
Figure 2: Bank of media filters. Photo: John Harvie
When a media filter is backflushed, the whole bed must be lifted by reversing the direction of water flow. To do this successfully, the flow rate during backflushing must exceed the filtration rate as the flow rate should continue to supply the field satisfactorily as well as give the extra flow needed to backflush. This should be accounted for when selecting a pump and motor.
One tank is flushed at a time using clean water from the other tanks for the backflush. Usually, one filter for backflushing is added to the number of filters needed to service the field. Two-tank systems are notorious for having problems during backflushing: the problems occur where there is not enough flow available to backflush properly and irrigate the field at the same time.
If the performance of media filters drops, tunnelling could have occurred, where preferential passages o flow have developed through the media and backflushing has been insufficient to lift the media adequately.
Using media filters in drip irrigation
Advantages
- Considered the most reliable filtration method and therefore often preferred for dirty water situations
- Three-dimensional filtration is created by sand and gravel of non-uniform size, thereby blocking particles of varying size.
Disadvantages
- Require a greater footprint than all other filter types
- Generally, require greater backflushing volumes than all other filter types
- Generally, more expensive than disc filters
- Generally higher-pressure loss across the filter.
Disc filters
Disc filters (Figure 3) can be considered a hybrid of screen and media filters. They generally have a series of grooved rings, forming a cylindrical filter with each groove crossing the other in different directions, creating a three-dimensional matrix of pathways. Different grades of filtering are achieved by varying the size of the grooves (usually specified by a particular disc colour), thereby representing an equivalent grade of filter mesh (table 3).
Colour | Blue | Yellow | Red | Black | Green | Grey |
---|---|---|---|---|---|---|
Mesh | 40 | 80 | 120 | 140 | 200 | 600 |
Micron (µ) | 400 | 200 | 130 | 100 | 55 | 20 |
Table 3: An example of disc filter filtration grades.
Source: Arkal Filtration Systems Filtration Product Guide, Netafim Australia.
Backflushing disc filters
For primary filtration, disc filters are automatically flushed with a series of internal jets. During backflushing, the discs are separated, water flow is reversed through multi-jet nozzles, the discs spin, and dirt is removed from the discs.
Using disc filters in drip irrigation
Advantages
- Significantly smaller backflushing volumes are produced compared with media filters
- Significantly smaller footprints are required compared with media filters
Disadvantages
- More moving parts than media filters, potentially creating more maintenance
- When the discs clog, the filter must be dismantled
- Discs need annual inspection, and if deemed necessary, require dismantling and manual cleaning.
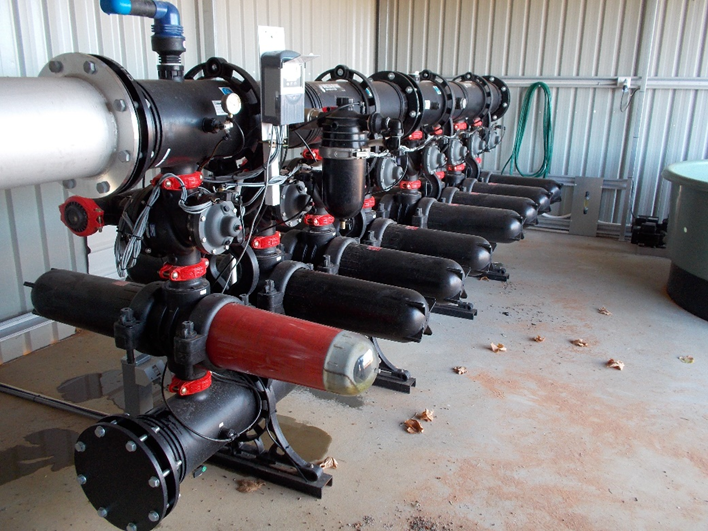
Figure 3: Disc filters. Photo: John Harvie
Hydrocyclone sand separators
Although not a true filter, Hydrocyclone sand separators (Figure 4) are often used before a filtration system to remove sand from groundwater extraction (50 microns or larger). They use centrifugal force to separate particles from water. If sand exists in water, it must not enter a drip irrigation system as sand does not decompose and cannot be dissolved or removed upon entering the emitter.
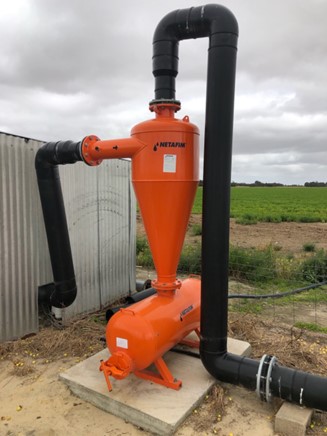
Figure 4: Hydrocyclone sand separator. Photo: Netafim Australia
Backflushing
Backflushing is generally conducted automatically, when a back-flush valve is triggered to reverse the water flow for a short period, removing collected debris into the backflush line.
Backflushing interval
Backflushing is either set on a time interval or pressure differential. In hot inland regions, media filters are usually set to backflush once every hour, while screen and disc filters may require backflushing two to three times per hour depending on water quality. Backflushing using a pressure differential is becoming quite popular. In this situation a pressure differential switch is installed over the inlet and outlet of the filter, to determine the pressure differential either side of the filter. Depending on flow rates, the head loss for clean filters is usually:
- 20–50 kPa for disc
- 5-20 kPa for screen
- 30-70 kPa for media filters.
Filters will experience an increasingly higher-pressure differential as they become clogged. The filter should be backflushed before the gauges register a larger pressure drop across the filter (disc filters 70 kPa, screen filters 50 kPa and media filters 100 kPa).
A combination of timed and pressure-differential backflushing is usually used, with the interval of timed backflushing set to trigger differential pressure first. This way filters still only backflush when required, minimising water lost to backflush, while also having timed flushing as a backup.
Monitoring the differential can also reveal screen filter damage or media filter tunnelling.
Remote monitoring of pressure differentials and backflushing events is also an option.
Backflushing volume
The amount of water ‘‘lost’ during backflushing is gaining attention as water resources become more limited and water authorities and councils look more critically at disposal options. Irrigators are beginning to consider backflushing water as a resource and are adopting one or more of the following measures:
- Pumping into a settling tank for re-use on farm
- Disposing onto woodlot, boundary vegetation, lawn or gardens if suitably located.
The backflush volumes generated with screen, disc and media filters vary. Generally, screen filter backflush water is 0.5-1% of the total water pumped, disc filter 0.5–1.5%, and media filter 2–5%, depending on water quality and whether backflushing is fully automated. While this volume does not appear to be large, consider the following:
Assuming 8.0 ML/ha is applied to a 10-hectare drip-irrigated property (80 ML total use), the total backflush volumes produced annually are:
Screen 0.4-0.8 ML
Disc 0.4–1.2 ML
Media 1.6–4.0 ML
These volumes are important when considering disposal options. Your irrigation designer should be able to provide you with estimates of backflush volumes upon request.
All automatic backflushing systems require ample pressure during backflushing, with no restriction on backwash pipework.
General filtration recommendations
- If you are concerned about irrigation water quality, have it analysed to determine the level of filtration necessary.
- Talk to irrigation designers, equipment suppliers and advisers before purchasing equipment.
- Make sure the filters are large or numerous enough to handle the system flow rate so that the pressure across a clean filter does not drop more than the head loss figures mentioned above. Allow for expansion of the irrigated area in a manifold design.
- Optimal filtration is achieved by using filters at the pump and backed-up with secondary filters in the field; that is, filtering twice.
Secondary filtration
Secondary filtration (back-up or check filters) serves as a backup to protect emitters from large amounts of dirt that can enter from breaks in the mainline, or small particles that were not removed by primary filtration which could aggregate to form larger particles, or growths within the system. Secondary filtration is generally designed to remove larger material (200 µ), therefore their mesh grade is usually one grade coarser, than the primary filters. If the primary filter is 120 mesh, secondary filtration is usually 80 mesh.
Screen or disc filters are used for secondary filtration. Secondary filters have traditionally been manually cleaned, requiring significant labour input when dirty water exists (Figure 5).
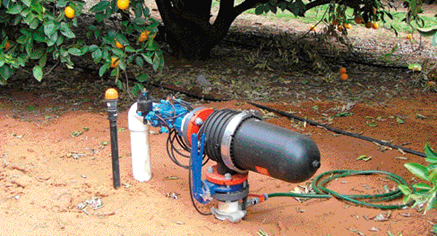
Figure 5: Back-up manually cleaned disc filter. Photo: Jeremy Giddings
Recently automatic (autoflush) and semi automatically cleaned screen filtration systems have become available. These are proving reasonably popular, although moving parts require additional maintenance (Figure 6).
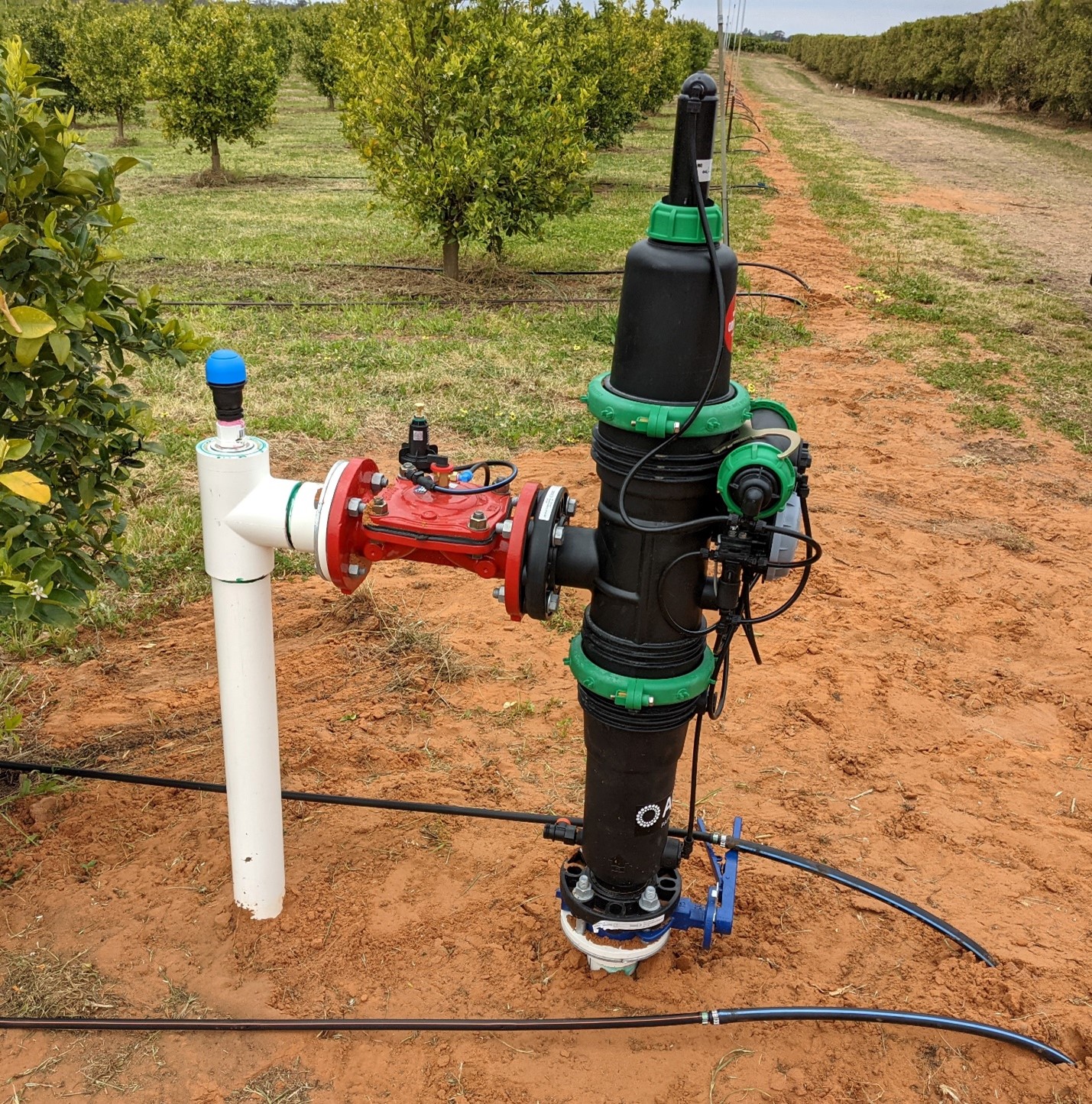
Figure 6: Back-up autoflush screen filter. Photo: John Harvie